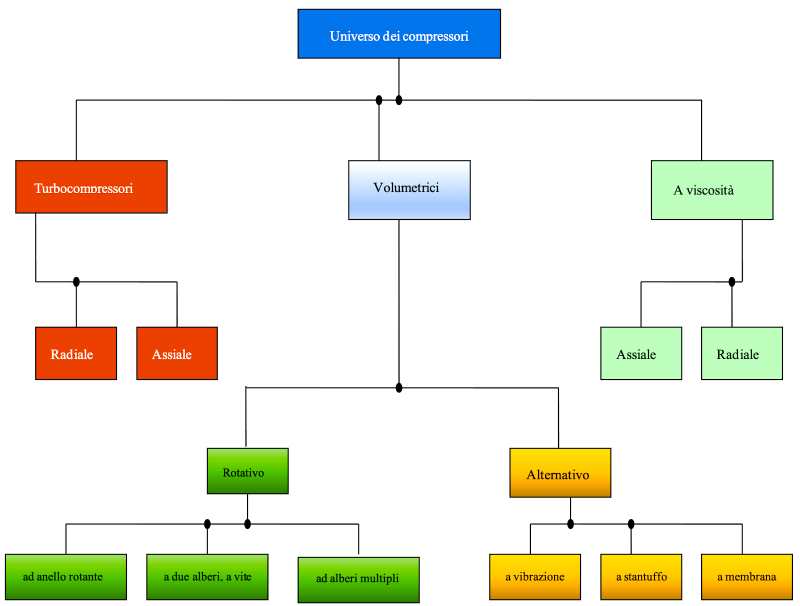
Cosa sono i compressori frigoriferi e quali sono le principali caratteristiche dei compressori alternativi? L’universo dei compressori frigoriferi è quanto mai variegato così come il loro impiego è differenziato, e generalmente la loro applicazione è basata sulla capacità frigorifera richiesta.
I compressori frigoriferi e la lubrificazione
Come abbiamo appena spiegato, il compressore è quell’organo meccanico che facendosi carico di una certa spesa frigorifera, innalza la pressione del fluido a quei valori necessari per ricominciare il ciclo frigorifero. Molti autori considerano il compressore il “cuore” dell’impianto anche se rappresenta una dei componenti più delicati dato che, contenendo un certo numero di parti meccaniche in movimento, un motore elettrico, un sistema di lubrificazione e un fluido refrigerante, deve garantire condizioni tali da soddisfare tutte queste esigenze. In questa trattazione prenderemo in considerazione solamente i compressori frigoriferi a pistoni e tra tutti quelli esistenti, solamente quelli a pistone alternativo tralasciando anche quelli con pistone a crociera, sia orizzontale sia verticale.
Quando si parla di compressore frigorifero, spesso non s’intende solo l’elemento “pompa” ma l’insieme composto da un elemento che genera il moto (normalmente un motore elettrico) a cui viene abbinata una pompa che ha lo scopo di aspirare dei gas in certe condizioni, comprimerli ad un determinato valore, per poi cederli in condizioni diverse. Per dimensionare un compressore in modo da ottenere una prefissata capacità frigorifera, occorre conoscere i concetti di cilindrata, potenza, rendimento volumetrico e isoentropico oltre ad avere una certa pratica con le leggi che governano questi fenomeni, senza poi tralasciare tutti i problemi inerenti alla lubrificazione, alla meccanica e ad un’altra quantità di nozioni che intervengono in questo campo. I compressori frigoriferi più comunemente usati nella refrigerazione appartengono alla gamma dei cosiddetti compressori volumetrici: si tratta del compressore alternativo a semplice effetto, (la cui meccanica ricorda, vagamente, il motore a scoppio) al quale il moto rotatorio viene trasmesso da un motore elettrico normalmente alimentato dalla tensione di rete. L’accoppiamento tra i due elementi (motore e pompa) è di norma rigido, anche se in passato si sono usati per moltissimo tempo trasmissioni a cinghia e pulegge. Nel caso di compressori ermetici o semiermetici l’accoppiamento è sempre di tipo rigido.
Mentre in un accoppiamento a cinghia e pulegge il compressore può ruotare entro una notevole gamma di giri, nel caso di accoppiamento rigido con trascinamento affidato ad un motore elettrico, il numero di giri è quello caratteristico del motore elettrico, che nella maggioranza dei casi sarà di 2950, 1450, 960, 700 giri al minuto a seconda che il motore elettrico sia rispettivamente a 2, o 4, o 6, o 8 poli. Prima di addentrarci nella descrizione dei fenomeni legati ad una serie di processi, occorre definire con precisione la terminologia adottata, così da non incorrere in malintesi.
La cilindrata dei compressori frigoriferi
La cilindrata del compressore è il volume generato dai pistoni durante ½ giro (180°) dell’albero motore detto anche albero di manovella. Tale valore si può calcolare nel seguente modo:
dove:
C = cilindrata del compressore [cm3]
d = alesaggio di un pistone [cm]
l = corsa del pistone [cm]
N = numero dei cilindri [-]
Volume orario generato
Il volume orario generato è il volume generato dai pistoni, nel loro moto alterno, ad un certo numero di giri, nell’arco di tempo di un’ora. Tale valore può essere calcolato nel seguente modo:
dove:
Vog volume orario generato [m3/h]
C cilindrata [cm3]
velocità di rotazione del compressore [giri/min]
Prima di proseguire con le altre grandezze caratteristiche, conviene richiamare schematicamente il funzionamento meccanico del compressore.
fig. 1 – Alcuni punti caratteristici del lavoro del compressore
- In questa fase, il pistone si trova nel suo punto più basso (detto punto morto inferiore) e, per via della depressione esercitata all’interno del cilindro, la valvola d’aspirazione è aperta, cosicché in tutto il cilindro si ha una pressione pressoché identica a quella d’aspirazione (pas).
- Il pistone riprendendo a salire e comincia a comprimere il gas aspirato, la pressione all’interno del cilindro aumenta ma non si è ancora raggiunto un valore sufficiente ad aprire la valvola di scarico. Nel frattempo, la valvola di aspirazione si è chiusa.
- Proseguendo nella sua fase di compressione, il pistone ha generato, all’interno del cilindro, una pressione (psc) sufficiente ad aprire la valvola di scarico. Tale pressione è data dalla pressione di condensazione esistente nell’impianto + una sovrappressione (necessaria a far sì che la valvola si possa aprire). In questo momento il gas comincia a defluire dall’interno del cilindro verso lo scarico. Il pistone non ha raggiunto il suo punto più alto (detto punto morto superiore).
- Lo scarico del gas dura fino a quando il pistone non raggiunge il punto morto superiore dato che in questo punto comincia anche la corsa di ritorno a cui corrisponde una riduzione della pressione all’interno del cilindro. Occorre notare che in questa posizione il cielo del pistone (ovvero la sua parte più alta) è leggermente distanziato dalla piastra valvole. In altri termini, tra cielo del pistone e piastra valvole vi è sempre un certo spazio, voluto dai costruttori per evitare che, a causa di dilatazioni, i due componenti entrino in collisione. Questo spazio, assieme ad altri, prende il nome di “spazio nocivo” ed è una delle cause di perdita di rendimento del compressore.
- A questo punto il pistone comincia a discendere ma la valvola d’aspirazione rimane ancora chiusa dato che la pressione esercitata da quel poco di gas che è rimasto racchiuso nello “spazio nocivo” non è ancora discesa al di sotto del valore della pressione d’aspirazione (pas). Durante la corsa di discesa del pistone, la pressione continuerà a diminuire fino a quando la valvola d’aspirazione non si aprirà. Questo accade quando la pressione è pari a quello d’aspirazione dell’impianto diminuito di una certa quantità che rappresenta la resistenza che oppone la valvola d’aspirazione all’apertura.
fig. 2 – aree che intervengono sulla valutazione del volume nocivo
Tra i volumi nocivi più importanti, notiamo quello relativo alla valvola di scarico (fig. 2 in colore rosso) che obbliga i costruttori di compressori frigoriferi ad utilizzare, per questo scopo, acciai particolarmente resistenti in modo da poter realizzare la piastra valvole più sottile possibile. Infatti, se lo spessore della piastra valvole diminuisce, diminuisce anche il volume nocivo generato dalla valvola di scarico. Questo tipo di soluzione è da ritenersi di gran lunga migliore rispetto a quella che prevede la riduzione del numero (o del diametro) dei fori destinati allo scarico dei gas.
La meccanica dei compressori alternativi
I compressori frigoriferi alternativi si possono suddividere in:
– Aperti
– Semiermetici
– Ermetici
Il compressore aperto è così chiamato perché un’estremità dell’albero a gomiti fuoriesce dal monoblocco fig. 3
fig. 3 – compressore aperto (per gentile concessione della ditta Bitzer)
Per evitare che il frigorigeno fuoriesca laddove l’albero di trasmissione esce dal carter, si rende necessario una particolare tipo di tenuta detta, in gergo, premistoppa. Dalla fig. 3 si vede come il compressore aperto può essere facilmente accoppiato con uno svariato numero di motori, non necessariamente di tipo elettrico. Una caratteristica peculiare di queste macchine consiste nel fatto che il fluido aspirato, non passa attraverso il carter, ma entra direttamente sulla testa. Al contrario, nel compressore semiermetico, il motore elettrico ed il meccanismo di pompaggio del gas, formano un corpo unico posto all’interno di un involucro imbullonato. In questo caso, quindi non è possibile adottare un diverso motore elettrico se non cambiando il modello del compressore.
fig. 4 – compressore semiermetico
Gli organi accessibili per una manutenzione ordinaria sono:
– la piastra valvole, a cui si accede smontando la testa;
– il carter dell’olio, a cui si accede o smontando la coppa (in alcuni modelli) o smontando la piastra frontale, in altri (con le dovute precauzioni, visto che detta piastra contiene, normalmente, una delle bronzine dell’albero a gomiti);
– smontando la piastra posteriore si può accedere al filtro meccanico e procedere a una verifica dello statore elettrico.
Nel compressore ermetico (fig. 5) il motore elettrico ed il compressore sono racchiusi in un involucro di acciaio saldato. L’involucro non può essere aperto per la manutenzione in loco. La differenza fondamentale tra questo compressore e uno semiermetico sta nella possibilità o meno di accedere al compressore e al gruppo motore.
fig. 5 – compressore ermetico sezionato
I compressori aperti sono generalmente azionati da motori elettrici però, come si è detto, possono essere accoppiati anche a motori a combustione interna, o all’albero motore dei motopescherecci, o ad una qualsiasi altra “presa di moto”. Normalmente, laddove si dispone d’energia elettrica, l’accoppiamento di un compressore aperto al motore si realizza tramite cinghie trapezoidali e pulegge. La velocità di rotazione del compressore dipenderà dal rapporto tra le pulegge e dal numero di giri del motore elettrico secondo l’uguaglianza
dove:
d1 diametro della puleggia traente [mm]
d2 diametro della puleggia trascinata [mm]
n2 numero di giri della puleggia trascinata [giri/min.]
n1 numero di giri della puleggia traente [giri/min.]
Di qui si può ricavare, per esempio che il numero di giri del compressore (n2) è dato da:
Il numero delle cinghie da utilizzare dipende sostanzialmente dalla potenza da trasmettere e dal tipo di cinghia che s’intende utilizzare e dal rapporto di trasmissione che identifica l’angolo d’avvolgimento. Un secondo metodo per trasmettere il moto al compressore è quello definito in gergo con il termine “accoppiamento diretto” dove tra l’albero del motore elettrico e quello del compressore è interposto un giunto. In questo caso il compressore sarà obbligato a ruotare alla stessa velocità del motore elettrico; il campo d’applicazione del complesso motore / compressore pertanto si restringe. Uno dei vantaggi di questa soluzione consiste nella minore usura del premistoppa dato che, in questo caso, l’albero del compressore gira in asse con il premistoppa e non è sottoposto alla trazione delle cinghie che portano, inevitabilmente, ad un’anomala usura di questo organo di tenuta. Come già accennato le applicazioni più comuni di questo tipo di soluzione, si trovano sulle corriere e sui camion refrigerati dove il moto viene prelevato direttamente dal motore endotermico. Le piastre valvole normalmente vengono realizzate in due modi: a lamella e ad anello.
fig. 6 due tipi di piastre valvole normalmente utilizzate per i compressori:
in alto: a lamella
n basso ad anello
La valvola a lamella (fig. 6 in alto) è costituita con acciaio armonico tranciato, e pertanto risulta particolarmente flessibile e leggera. Al di sopra della piastra sono poste le valvole di scarico, mentre al di sotto c’è quelle di aspirazione. La parte della valvola che assolve alla funzione di aprire o chiudere le luci (di aspirazione o di scarico) è, normalmente, quella terminale che ha forma circolare come la luce a cui sovrintende, mentre la parte restante, detta gambo, serve a migliorare le caratteristiche d’elasticità. Una volta che la valvola si apre, il ritorno “in sede” avviene infatti sfruttando l’elasticità del materiale con cui è costruita. Quando all’interno del cilindro si crea una pressione pari alla pressione di scarico dell’impianto la valvola non si apre ancora, perché vi resta da vincere, la pressione generata dalla tensione del materiale di cui la valvola è composta. Quando la pressione all’interno del cilindro sarà pari alla pressione di condensazione + la pressione dovuta dalla tensione del materiale + quella dovuta al peso della valvola, la valvola viene forzata ad alzarsi dal piano di appoggio e quindi ad aprire il passaggio del gas attraverso i fori. Un discorso analogo (ma con pressioni decrescenti) vale per la valvola d’aspirazione. In questo caso il peso della valvola gioca in maniera favorevole all’apertura. Le valvole ad anello, mostrate nella figura 11 in basso, sono realizzate in acciaio armonico come quelle precedentemente viste, pur esistendone anche di altro tipo, fatte con anelli di metallo pesante; in questo caso, la valvola ad anello viene mantenuta normalmente nella posizione chiusa mediante delle molle, mentre l’apertura avverrà nelle stesse condizioni precedentemente viste.
Leggi anche le parte precedenti del corso per frigoristi sui principi della termodinamica:
Condividi l'articolo
Scegli su quale Social Network vuoi condividere